Researcher Linsey Marr evaluates efficacy of sterilized N95 respirators, alternative mask materials in filtering particles
May 19, 2020
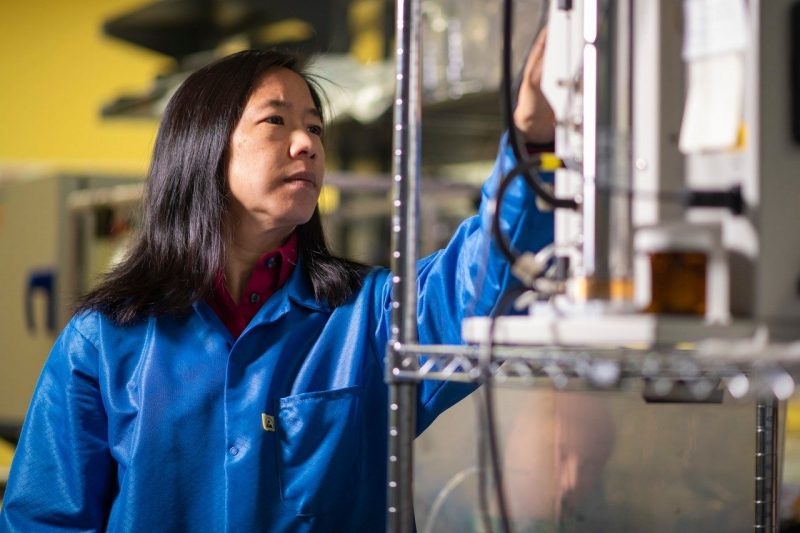
FROM VT NEWS | MAY 19, 2020
Since March, Virginia Tech civil and environmental engineering professor Linsey Marr, an expert in the airborne transmission of infectious disease, has been testing the efficacy of sterilized N95 respirators and alternative mask materials in filtering out particles.
The rapid science experiments conducted by Marr’s team aim to help quantify how well these forms of personal protective equipment shield their wearers against COVID-19, especially in the face of shortages.
Dealing with sluggish PPE supply chains, the medical community and the wider public have turned to improvisation. Some hospitals have worked to extend the use of their stores of N95 respirators by sterilizing them. Members of the public, advised by the Centers of Disease Control and Prevention to wear masks in places like grocery stores and pharmacies, are also exploring creative problem-solving by sourcing off-the-shelf materials for homemade masks. As these groups adapt, Marr’s team is working to supply them with insights grounded in science.
When testing sterilized N95 respirators, Marr and graduate students Jin Pan and Charbel Harb, members of Applied Interdisciplinary Research in Air (AIR2) Laboratory and fellow civil and environmental engineering professor Hosein Foroutan’s Applied Interdisciplinary Research on Flow Systems (AIRFlowS) Laboratory, found that the respirators retained their ability to filter particles after up to 10 cycles of sterilization by hydrogen peroxide vapor and by ethylene oxide.
“Since I understand how the coronavirus moves around in air, I knew how important it was for health care workers to have proper respiratory protection,” said Marr, the Charles P. Lunsford Professor of Civil and Environmental Engineering. “I knew my lab could help by testing N95s after sterilization to ensure that they could be reused safely. I quickly wrote up a procedure, and my students reconfigured our equipment to start running experiments.”
Marr’s research looks more broadly at the sources, transformations, and fate of air pollutants. Over the years, she’s focused on engineered nano-materials and viral aerosols — mainly those of the flu for the latter — and how they can be physically and chemically transformed in the environment. As she’s pivoted in recent months to apply her insights to the novel coronavirus, Marr, a GCC affiliate, has weighed in on subjects that have captured national media attention, such as the possibility of transmission by inhalation, the 6-foot distance recommendation for running outside, and how virus particles may or may not land on a person’s clothes or other surfaces.
In their look at homemade mask materials, Marr’s team has tested items that have emerged in the public eye in recent months. So far, they’ve tested materials that include Shop-Vac bags, HVAC filters, T-shirts, microfiber cloth, felt, auto shop rags and towels, and coffee filters.
A few top performers and busts emerged from their tests. Microfiber cloth, a material used to clean eyeglasses, filtered out at least 80 percent of particles under optimal conditions, while a heavyweight cotton t-shirt, a shop towel, and a shop rag filtered out only about 10 percent of the hardest particles to remove, and about 50 percent of the larger ones. HVAC filters removed a low of 20 percent of particles; Shop-Vac bags removed at least 60 percent.
The experiments are ongoing, but Marr has been releasing the results in real time on Twitter. She also shared the procedure behind the tests on Twitter, and other aerosol science labs around the country have since adopted these methods to help test materials in their regions.
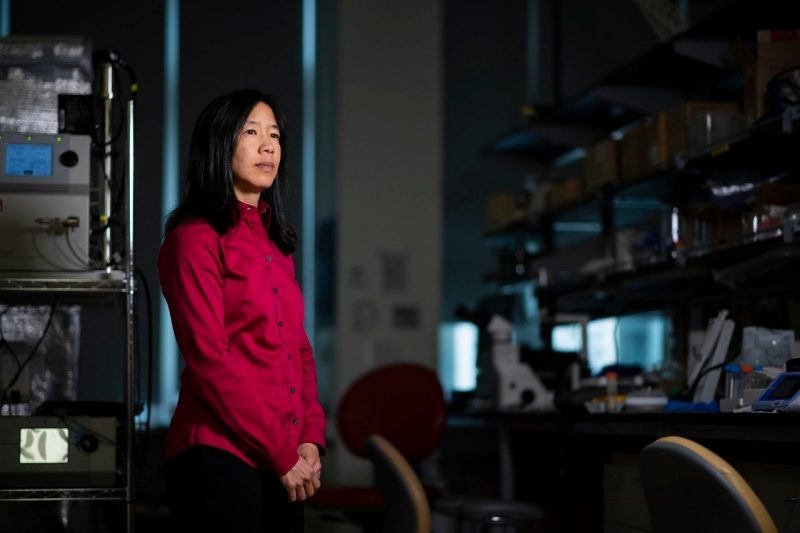
The team’s experiments on sterilized N95 respirators were fueled largely by requests from local medical professionals, like Anthony Baffoe-Bonnie, Carilion Clinic’s medical director of infection control and an epidemiologist for the hospital, and infection preventionist Maimuna Jatta.
Baffoe-Bonnie’s team wanted to know if the hospital’s N95 respirators retained their filtration efficacy after up to 10 cycles of sterilization using hydrogen peroxide vapor, a common technique among hospitals. There was added uncertainty in that the Carilion team’s machines use a stronger concentration of hydrogen peroxide than the methodology referenced in the publications they read for guidance.
Marr’s tests showed that the N95 respirators retained their efficacy post-sterilization with the technique, helping the team solidify their procedure. “With that, we knew we could use what we had,” said Baffoe-Bonnie. He said he was grateful to have Marr and her testing resources close by. “I think she’s a godsend in that regard,” Baffoe-Bonnie said. “We had a student drive the stuff over to her, and we had our results back — it couldn’t have been faster.”
Marr’s lab is set up to evaluate filtration efficacy of porous media for particles ranging in size from 0.04 to 1.0 microns. Within that capacity, the team can assess how well a form of PPE meets the standard for N95 respirators, which are required to block at least 95 percent of particles 0.3 microns in diameter.
To test materials, the team sprays sodium chloride particles from a liquid salt solution into a large bag and measures the number and sizes of the particles in the bag. They then use a vacuum pump to pull air containing the particles through the respirator, mask, or material they’re testing, and measure the number and sizes of particles that made it through to the other side.
“The mask or filter removes particles, and we measure hopefully much less than what’s in the big bag,” explained Marr.
In a sea of homemade mask materials, learning which options sink or float
Some of the alternative mask materials arrived in Marr’s lab for testing via Matt Hull, a research scientist at the Institute for Critical Technology and Applied Scienceand Marr’s colleague on the institute’s NanoEarth team. Hull, who earned his master’s and doctoral degrees from Virginia Tech, has worked extensively with Marr and other researchers to understand how nanoscale materials move through the environment and what happens when we’re exposed to them.
Hull recognized that amid the COVID-19 pandemic, there would be a strain on supply chains for protective materials with specialized properties, including materials that the medical community might eye for last-resort use in PPE. He searched for products that might reproduce some of the functionality of certified PPE materials, but could be bought off the shelf.
Hull dropped off potential candidates at the Kelly Hall headquarters of the Institute for Critical Technology and Applied Science, where a conference room that, under normal circumstances, would be booked for committee meetings and thesis defenses was transformed into a staging area for piles of material destined for testing in Marr’s lab down the hall. Hull and the other researchers would exchange text messages when materials were ready for pickup, cobbling together a socially distanced courier service.
“As a scientist, you work your whole life and you go home a lot of nights, and you think, ‘What did I do today?’” said Hull. “‘I maybe edited a paper, sent a few emails.’ You rarely get the chance to contribute so directly to solving a problem.”
Marr’s team has also begun testing several leading, open-source 3D-printed mask designs submitted by Chris Williams, a mechanical engineering professor who has helped coordinate a campus-wide effort to test, design, and produce PPE, ventilator components, and other COVID-19 medical supplies. His lab will base their next steps in PPE production on Marr’s tests.
Her team will continue to run experiments as new ideas for mask materials surface. “We’ll keep testing materials as long as what we’re doing hasn’t been done by other people,” Marr said.
In immediate response to the COVID-19 pandemic, Virginia Tech faculty, staff, and students have initiated numerous research projects with local and global salience. Learn more from the Office of the Vice President for Research and Innovation.
– Written by Suzanne Irby and Eleanor Nelsen
CONTACT:
Suzanne Irby